Model-Based Control of Micro Gas Turbines
The increasing need for high energy density portable power devices has led to intense research and development efforts on micro gas turbine systems with power outputs from a hundred up to a few kilo Watts. Gas turbine generator sets offer advantages over battery based portable power systems due to the higher chemical energy density of fuel and faster refill procedure. Such systems need smart control for fuel efficient and reliable operation.
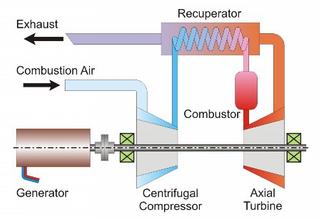
For the purpose of model-based control and fault detection a control oriented model (COM) is necessary. A COM models the input-output behaviour of the micro gas turbine system with reasonable precision at low computational complexity. It is designed to include explicitly all relevant transient effects and is represented by a set of nonlinear ordinary differential equations, which are derived from physical first principles.
Faults in a control loop of a micro gas turbine are particularly important since feedback from a faulty sensor or actor quickly result in instability causing a complete failure of the device. Such faults might need to be detected within just a few samples. Therefore it is important that faults are detected during normal operation of the gas turbine, without the need to perform any additional tests to perform the diagnosis.
The gas turbine process is regulated by a controller and the known variables consist of controller outputs and sensor data. Such a situation is depicted in the following Figure, which also illustrates a fundamental complication faced by the diagnosis system designer. Disturbances, also called unknown inputs, and considered faults also influence the process. The diagnosis system must be capable of separating the influences caused by these unknown inputs and the faults. A certain redundancy is thus needed to detect and isolate faulty components. The detection and isolation of actuator as well as sensor failures will be done with the multiple model adaptive estimation method (MMAE). This algorithm is composed of a bank of parallel Kalman filters, each matched to a specific hypothesis about the failure status of the system. Where necessary, certain Kalman filters in the filter bank will be replaced by an extended Kalman filter.
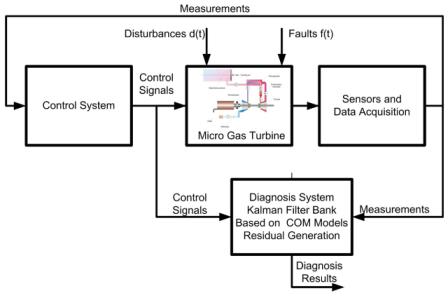