Hybrid Pneumatic Engine
The hybrid pneumatic engine concept developed at IDSC uses compressed air as energy buffer and allows for substantial downsizing of engines. Both measures lead to an increased efficiency and an excellent driveability of the automotive propulsion system. Hybrid pneumatic vehicles are expected to be much cheaper than hybrid electric vehicles since no batteries or electric motors are needed.
The project team has realized the world's first fully functional hybrid pneumatic engine. The researchers have proven that this new engine concept saves around 30% fuel compared to conventional gasoline engines with the same power.
Detailed Project Description
Overview paper of the project
DownloadGerman (PDF, 1.2 MB)vertical_align_bottom Source: Motortechnische Zeitschrift (MTZ) Vol.71(1), 2010, pp. 52-58
DownloadEnglish (PDF, 1.2 MB)vertical_align_bottom Source: MTZ Worldwide Vol.71(1), 2010, pp. 38-44
Poster of the project (presented at Singapore International Energy Week 2009):
DownloadPoster (PDF, 7 MB)vertical_align_bottom
In spite all of its well-known problems, the internal combustion engine (ICE) continues to be the most important means of automobile propulsion and is expected to remain so for several decades. However, its fuel consumption and consequent CO2 emissions are symptomatic of major system-inherent problems. First, the vehicle’s kinetic energy cannot be transformed back into chemical orother usable energy when braking. Second, consumer demand for high maximum power leads to increased engine displacement. The mean efficiency of the propulsion system is consequently decreased, since internal combustion engines exhibit a low efficiency at part load. Third, a fast and convenient engine startup with a conventional starter after a short vehicle standstill is not possible. This prevents shutting off the engine beforehand and thus leads to additional fuel consumption during idling.
Automobile manufacturers are currently attempting to tackle these problems by focusing on hybrid electric vehicles (HEVs). Some research groups, however, have been investigating another alternative, namely the pneumatic hybridization of ICEs.
The basic idea of pneumatic hybridization is to use the ICE not only for combustion, but also as a pump and a pneumatic motor. All other known hybrid propulsion systems require additional separate devices for energy conversion, a fact that drives up cost.
For pneumatic hybridization, each cylinder of the ICE is connected via a fully variable charge valve to a shared air pressure tank.
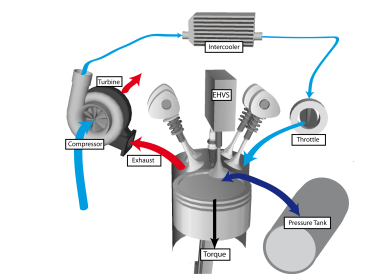
In vehicle braking phases with fuel cut-off, the engine can intake air and pump it into the pressure tank. Without the injection of fuel, the pressurized air can then be used again for starting or driving the vehicle. Shifting the operating point of the engine is also possible, using at least one cylinder in a conventional combustion manner at a high load and using at least one cylinder to pump air into the pressure tank. The pressurized air can also be used to boost the conventional engine combustion mode, thereby overcoming the turbo-lag in supercharged engines.
The pneumatic hybridization of an internal combustion engine is possible for both spark ignition (SI) and compression ignition (CI) engines.
The hybrid pneumatic engine (HPE) was long thought to be a system in which all engine valves had to be actuated in a fully variable manner to allow for two-stroke pneumatic modes and still enable the four-stroke combustion mode. However, this setup adds complexity and cost. During this project, the authors patented the idea to stick to four-stroke cycles for both combustion and pneumatic operations. The intake and exhaust valves remain camshaft-driven and only the charge valve, which connects the cylinders to the pressure tank, is fully variable. An overview for the valve actuation is given in Figure 2.
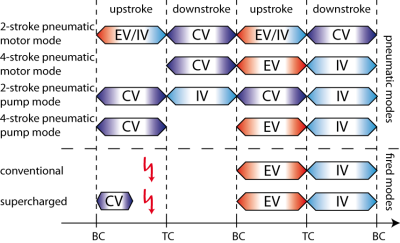
The fuel consumption calculations all use the quasi-static simulation technique. The supervisory control deciding on which engine mode to use is based on the deterministic dynamic programming (DP) technique. It yields the optimal control sequence for a given drive cycle while guaranteeing charge sustenance. Due to its optimality, this technique provides a benchmark for the hybrid propulsion system, because it ensures comparability.
All fuel consumption calculations were carried out for the MVEG-95 driving cycle. To ensure comparability between gasoline and diesel engines, the amount
of CO2 savings relative to the 2.0l naturally aspirated (NA) SI engine is chosen as a measure instead of fuel savings. The results are shown in Figure 3.
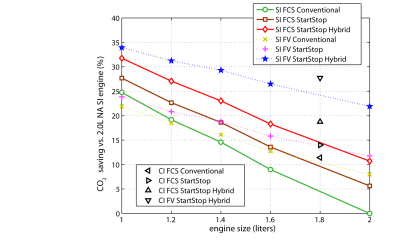
Several points should be noted:
- Downsizing a gasoline engine can save as much fuel (and CO2) as 25%. It is the most important contribution to the overall fuel gain. Note that without the HPE concept, the “turbo-lag” would be an issue.
- The pneumatic hybridization for an engine system based on fixed camshafts for intake and exhaust valves in combination with downsizing the gasoline engine yields overall fuel savings of 32%. Note that the “hybridization gain” of 7 percentage points is just a small share of the overall fuel gain. Part of this hybridization gain comes from using the pneumatic motor mode instead of the conventional mode, using tank energy that was stored during recuperation or recharge. The other part comes from avoiding engine idling by utilizing engine stops with subsequent pneumatic starts. The fuel savings resulting from downsizing and applying start/stop is also shown in Figure 3.
- An overall amount of fuel savings of 34% is achieved when considering a downsized camless gasoline engine with pneumatic hybridization and cylinder deactivation.
- The conventional diesel engine produces less CO2 than the baseline gasoline engine with the same maximum power. However, for the hybrid pneumatic diesel engines, the overall amount of CO2 savings is lower than for downsized hybrid
gasoline engines. The main explanation for that is that the diesel engine cannot be downsized any further.
The most important result of this investigation is that the effect of downsizing the engine is much more important than the hybridization itself.
The HPE concept features the supercharged mode, offering the option to inject pressurized air from the tank into the cylinder during the compression phase.
This enables the injection of additional fuel for both PFI and DI engines, providing the fastest torque response possible using the air path of the ICE. This mode is always available as long as the tank pressure is higher than the desired boosting pressure. Using regenerative braking or the recharge modes, this tank pressure can be guaranteed for almost all driving conditions.
The supercharged mode is especially helpful for overcoming the so-called “turbo-lag” in supercharged engines, since they typically respond slowly to a demanded torque step at low engine loads and speeds. Once the torque increases by activating the supercharged mode, the engine exhaust enthalpy is increased, thereby propelling the turbine of the turbocharger. Since the accelerating compressor of the turbocharger leads to an increased intake pressure, the additional air from the tank is needed only for a very short time.
The HPE concept is assumed to not affect emissions and the added cost is rather low. The advantages of the concept are the excellent driveability and the improved fuel consumption, especially when considering the downsizing effect.
The HPE concept is especially effective when it is combined with the idea of heavy downsizing and supercharging SI engines. The synergy effects of these
two concepts are evident.
For this project, a downsized and supercharged gasoline engine was chosen to be modified into an HPE. It is a two-cylinder multi-purpose engine (MPE750) with a displaced volume of 0.75 liter. In its original form, the engine was designed by Wenko Swissauto AG, manufactured by Weber Automotive GmbH. The engine has a compression ratio of 9.0, and it uses port fuel injection. The engine normally uses a GT12 turbocharger. For this project, however, the turbine of the turbocharger was replaced by a GT14 turbine to reduce the engine’s backpressure and thus enhance the efficiency at high speeds. Normally this would result in a high turbo lag but due to the availability of the supercharged mode, this issue vanishes. The engine modifications for the pneumatic hybridization were made in cooperation with Wenko Swissauto AG.
For the engine modification, the fixed camshaft configuration was chosen. The fully variable valve actuation for the charge valve was realized using the Bosch electro-hydraulic valve system (EHVS). The chosen engine normally has two intake and two exhaust valves per cylinder. It was decided to replace one exhaust valve per cylinder by a charge valve that is actuated by the EHVS. A picture of the modified engine is shown in Figure 4:
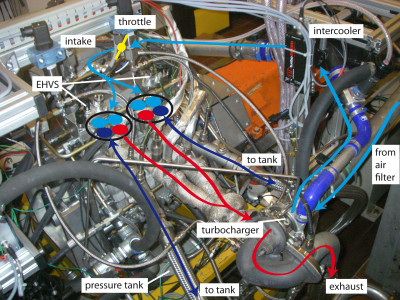
Figure 5: Testbench Structure
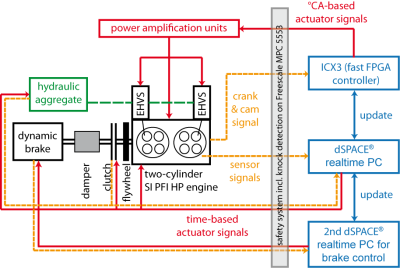
The engine was modified successfully and all conventional and new engine modes could be tested: Pneumatic motor mode, pneumatic pump mode, rapid pneumatic start. However, the most important result is the switch from the conventional mode to the supercharged mode. The resulting instantaneous torque response is shown in Figure 6:
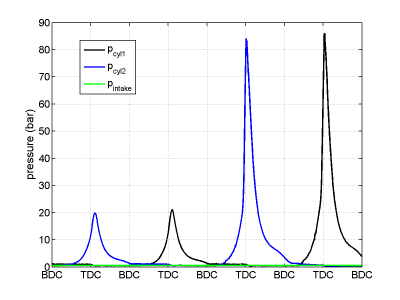
Using this supercharged mode, the turbo lag of the engine can be overcome. A measurement of this is shown in Figure 7:
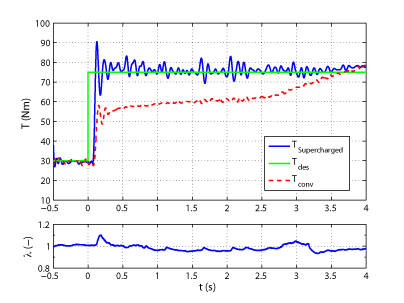
The pneumatic modes were optimized for efficiency and all mode changes could be implemented. Consequently it was possible to measure the engine's fuel consumption on driving cycles, such as the New European Driving Cycle. The dynamic brake emulates the behavior of a real vehicle. For an emulation of the VW Polo, see Figure 8. The bottom part of the figure shows the allowed deviation from the desired speed and the actual deviation.
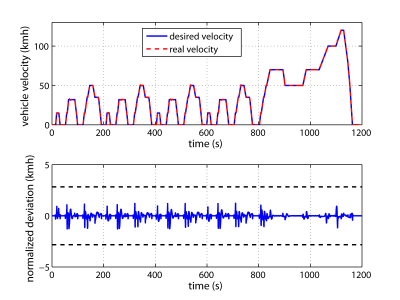
The driver mode switches and engine mode switches as well as the tank pressure signal and the cumulated fuel mass for this drive cycle experiment is shown in Figure 9.
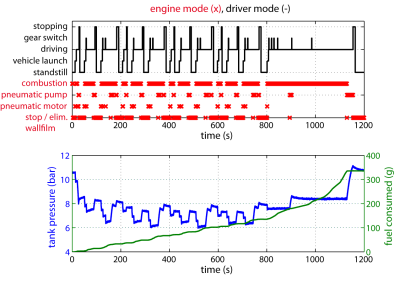
Tests on the New European Drive Cycle have proven that this technology saves between 25% and 35% fuel depending on the vehicle. For the comparison, the engines have the same rated power and the same vehicle as a basis. Figure 10 shows all the results for the New European Drive Cycle:
Goals of the Project
Forthcoming work will focus on the further optimization of the supercharged mode and a more advanced low-level control structure.
The final goal of this project is the integration of a hybrid pneumatic engine into a passenger car to demonstrate the driving performance and the fuel consumption. For this task, a cooperation with an automobile manufacturer is sought.
System Design and Analysis of a Directly Air-Assisted Turbocharged SI Engine with Camshaft Driven Valves, Voser C., Onder C., and Guzzella L.,Energies 2013 (6), pp. 1843-1862
Intake Manifold Boosting of Turbocharged Spark-Ignited Engines, Zsiga N., Voser C., Onder C., and Guzzella L.,Energies 2013 (6), pp. 1746-1763
Design Methodology of Camshaft Driven Charge Valves for Pneumatic Engine Starts, Moser M., Voser C., Onder C., and Guzzella L.,Proceedings of IFAC Workhshop ECoSM, 2012
System Design of a Directly Air Assisted Turbocharged SI Engine Using a Camshaft Driven Valve, Voser C., Diss. ETH No. 20706, 2012
System design for a direct-boost turbocharged si engine using a camshaft driven valve,”, Voser C., Onder C., and Guzzella L., FISITA 2012 World Congress, 2012
In-cylinder boosting of turbocharged spark-ignited engines. Part 2: Control and experimental verification, Voser C., Ott T., Dönitz C., Onder C., and Guzzella L., Proc. IMechE, Part D: J. Automobile Eng., Vol. 226(11), 2012, pp. 1564-1574
In-cylinder boosting of turbocharged spark-ignited engines. Part 1: Model-based design of the charge valve, Voser C., Dönitz C., Ochsner G., Onder C., and Guzzella L., Proc. IMechE, Part D: J. Automobile Eng., Vol. 226(10), 2012, pp. 1408-1418
Turbocharged reciprocating piston engine having a conducted pressure tank for bridging the turbo lag, and method for operating said engine / Turboaufgeladene Hubkolbenkraftmaschine mit angeschlossenem Drucktank zur Turbolochüberbrückung und Verfahren zum Betrieb derselben, Dönitz C., Voser C., Onder C., Guzzella L., Patent Application WO/2001/015336
Validation of the Fuel Saving Potential of Downsized and Supercharged Hybrid Pneumatic Engines Using Vehicle Emulation Experiments, Dönitz C., Voser C., Vasile I., Onder C., and Guzzella L., Journal of Engineering of Gas Turbines and Power, Vol. 133, Iss. 9, 2011
Das Downsizing-Boost Konzept auf Basis der pneumatischen Hybridisierung von Ottomotoren / The pneumatic hybridization concept for downsizing and supercharging gasoline engines, Guzzella L., Onder C., Dönitz C., Voser C., Vasile I., Motortechnische Zeitschrift (MTZ) Vol.71(1), 2010, pp. 52-58
Hybrid Pneumatic Engines, Dönitz, C., Diss. ETH No. 18761, 2009
Realizing a Concept for High Efficiency and Excellent Driveability: The Downsized and Supercharged Hybrid Pneumatic Engine, Dönitz C., Vasile I., Onder C., Guzzella L., SAE 2009-01-1326, presented at SAE World Congress 2009
Dynamic Programming for Hybrid Pneumatic Vehicles, Dönitz C., Vasile I., Onder, C., Guzzella, L., Proceedings 28th American Control Conference (2009), pp.3956-3963
Modelling and Optimizing Two- and Four-Stroke Hybrid Pneumatic Engines, Dönitz C., Vasile I., Onder, C., Guzzella, L., Proc. IMechE, Part D: J. Automobile Eng., Vol. 223(2), 2009, pp. 255-280
Pneumatic Hybrid Internal Combustion Engine on the Basis of Fixed Camshafts, Dönitz C., Vasile I., Onder, C., Guzzella, L., Higelin P., Charlet A., Chamaillard Y., Patent Application WO/2009/036992 (filed 9/2007)
Rapid Start of Hybrid Pneumatic Engines, Vasile I., Dönitz C., Voser C., Vetterli J., Onder C., Guzzella L., Proceedings of the IFAC Workshop ECoSM 2009, pp 123-130
03.06.10
external pageInterview with Prof. Guzzellacall_made
At the KPMG grant award ceremony, Prof. Lino Guzzella explains the HPE technology and its advantages to the public.
17.05.10
external pageServus TV (Austria)call_made
reports about the Hybrid Pneumatic Engine (starting at 4:09 minutes). The report focuses on the cost advantages compared to hybrid electric vehicles.
07.01.10
external pageSF Tagesschaucall_made
The swiss television reports about the Watt d'Or Award 2010 for the HPE in the category energy efficient mobility.
21.04.09
external pageHPEVideo on YouTubecall_made
This video shows the hybrid pneumatic engine at IDSC in action, the new european driving cycle is emulated. The control and surveillance panels are shown, and the engine sound for different engine modes can be heard.
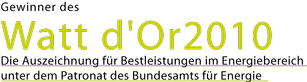
The hybrid pneumatic engine team has won the Watt d'Or Award in the category energy-efficient mobility
DownloadENERGEIA Magazine special edition Watt d'Or 2010 (PDF, 1.2 MB)vertical_align_bottom
external pageVideo Tagesschau SF 07.01.2010call_made
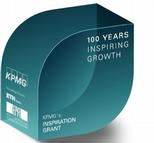
The Hybrid Pneumatic Engine Team was awarded the KPMG Inspiration Grant 2010.
external pageKPMG Media Releasecall_made
external pageVideo: Interview with Prof. Guzzellacall_made
16.05.11 external pageAuto Bildcall_made
04.06.10 ETH Life
17.05.10 external pageServus TV (from 4:09)call_made
08.01.10 ETH Life
07.01.10 external pageTagesschau (SF)call_made
07.01.10 external pageBundesamt für Energiecall_made
02.11.09 external pageIEEE Spectrumcall_made
26.06.09 ETH Life
26.06.09 external pageTagesanzeigercall_made
25.06.09 external pageTagesschau (SF)call_made
25.06.09 external pageDIE ZEITcall_made
04.06.09 external pageThe Economistcall_made
11.02.09 external pageMIT Technology Reviewcall_made
04.02.09 external pageScience Dailycall_made
27.01.09 ETH Life
12.10.08 external pageNeue Zürcher Zeitungcall_made
7.6.2013
Congratulations! Michael Moser and Christoph Voser have been awarded the Second Place Zuger Wissenschaftspreis 2013 for the Master Thesis "Boost Mode Torque Control and Pneumatic Start for Hybrid Pneumatic Engines".
29.1.2013
Congratulations! Norbert Zsiga was awarded the SGA Förderpreis for his outstanding Master thesis "Indirect Boosting of Turbocharged SI Engines".
18.04.2011
Congratulations! Gregor Ochsner was awarded the ETH-Medal for his outstanding Master Thesis "Valve Design and Torque Control of a Hybrid Pneumatic Engine with Camshaft Driven Charge Valves".
14.01.2011
Congratulations! Christian Dönitz has been awarded the ETH Medal 2010 for his outstanding dissertation "Hybrid Pneumatic Engines".
18.11.2010
Congratulations! Christian Dönitz has received the external pageHermann-Appel-Prizecall_made 2010 for his dissertation "Hybrid Pneumatic Engines".
18.06.2010
Congratulations! Stephan Zentner won the award external pageDiplomandenpreiscall_made 2009 from the SEW-EURODRIVE-Foundation for his master thesis "Supercharging a Pneumatic Hybrid Engine (PHybE) - Design, Identification and Control".
03.06.2010
The hybrid pneumatic engine team has been awarded the KPMG Inspiration Grant. The grant honours projects which make a socially relevant contribution to the benefit of future generations.
29.04.2010
Tobias Ott was awarded the ETH-Medal for his outstanding Master Thesis "Hybrid Pneumatic Engine using Camshaft driven Charge Valves".
07.01.2010
The hybrid pneumatic engine team has won the Watt d'Or Award 2010! This national prize was awarded by the Swiss Federal Office of Energy in the category energy-efficient mobility.